THE FUTURE IS PREFABRICATED: TIMBER-FRAME STRUCTURE BUILDINGS MANUFACTURED INDOORS
- Miradex Team
- Jan 13, 2022
- 5 min read
A very versatile structural system that is dedicated to energy-efficient, resilient, durable, and eco-friendly houses
Introduction
The technological progress in the last 50 years has had, has, and will keep on having a significant impact on almost all industries, whether we are talking about products or physical and technological services. The civil engineering sector was not left behind and progress on multiple aspects have been recorded: high-performance building materials, more efficient constructive systems, advanced software for design, equipment, and installations with a reduced energy consumption…and last but not least, machines that replace human labor in the process of building.

In this article, we will briefly take a look at what building a house through prefabricating the building elements, especially the timber frame structural system, means.
About prefabrication
As its name implies, it is the constructive system through which most construction elements of a building are manufactured on another site than that of the building (off-site), generally a production hall, then they are transported and assembled on the construction site (on-site), after a carefully organized plan. A big part of the processes is moved into the hall, where productivity and the quality of the building increase, while costs and risks drop.
According to this report, through prefabrication:
production lead time is reduced by 65%
costs drop by 45% (materials consumption, logistics, manual labor, unexpected expenses, etc)
results 75% fewer malfunctions;
Why? Because, in a production hall, the internal environment is controlled and it is suitable for working no matter the season, the small and qualified staff operates as machines that do most of the hard work, the quality control is secured by the following of well-planned processes and procedures and the respective costs are reduced through repetition and optimization. More than that, material cost is also reduced by the limitation of manufacturing waste ( especially wood), which happens especially due to the correlation between design and manufacturing in specialized software.

Therefore, many processes that would usually be carried out simultaneously on the construction site, by many teams, are directly influenced by the weather conditions, the level of training of the construction staff and on-site organization, and unexpected events that are much more likely to happen on-site than in a hall.
According to Offsite Construction Hub, there are 3 types of prefabricated modular building techniques:
Volumetric Modular Constructions: compact wooden or metal structure modules that include thermal insulation, installations, finishes, or even furniture- 50-60% more efficient than the conventional construction techniques. An example is the natural modular house NIDUS Home.
Hybrid constructions: volumetric elements and prefabricated panels- 30-40% more efficient than the conventional construction techniques
Prefabricated panels: from different structural materials (CLT, Timberframe, Light Steel Frames, etc) – 20-30% more efficient than the conventional construction techniques, depending on the equipment level of the panels.
Timber frame system prefabricated house
The timber frame structural system ( translated from English “wooden frame”) is a relatively simple solution for construction and it involves multiple load-bearing wooden frames, of various sizes and widths, that assemble the structure of the house. There are more constructive options:
1. The simple structure: the frames/ prefabricated wooden panels that assemble the walls of the house are transported to the construction site, then they are plated, insulated, and finished. They take a lot of on-site work, and generally, there is no need for a crane in setting them up.
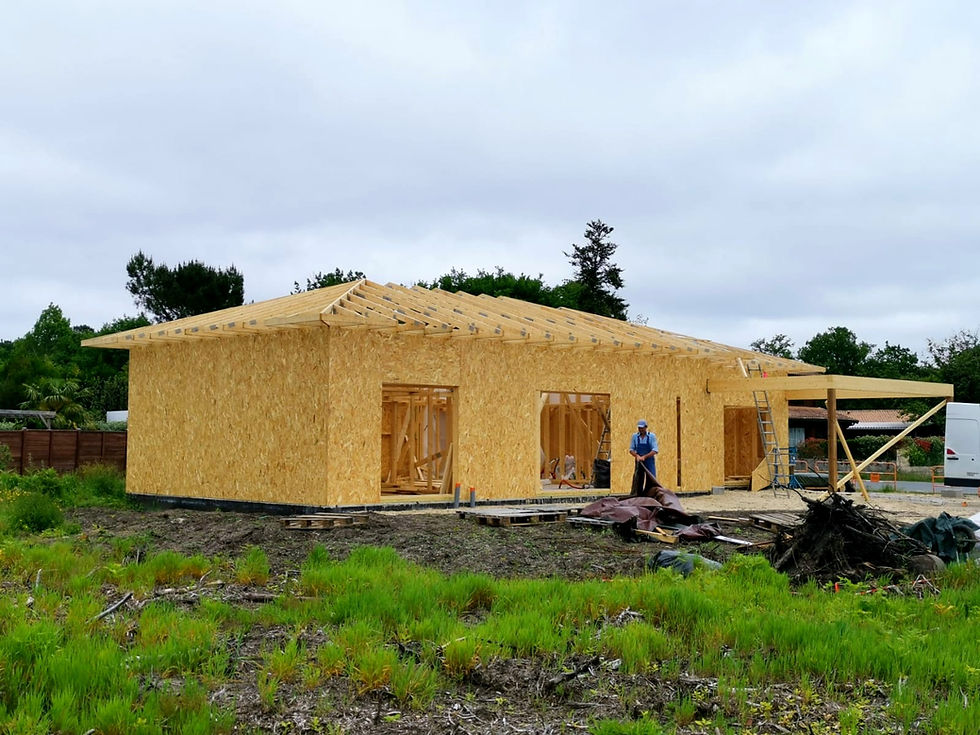
2. Plated and insulated structure: the panels that form the house are insulated and plated on one or both sides along with the membranes and respective foils ( e.g. internal vapor barrier) from the factory and they can include electric wiring with sockets. A crane is needed for handling and this requires less work on-site.

3. Complete structure: it can involve the external finish ( wooden façade), window panes, wiring, pipes and ductwork and if necessary, even the internal finish, depending on the chosen solution. In this scenario, more attention to transport and assembly is needed, but the great advantage is that work on-site is almost just a simple large-scale lego game

Besides the structure of the walls, a house also involves floors between levels and the roof, which can be a simple roof or an attic. In the case of these structural elements, there are optimized prefabricated solutions:
Posi-Strut floors or latticed wooden floors with MiTek connectors are a very efficient solution from multiple perspectives: they are lightweight compared to a concrete slab, but they are rigid and resilient to loadings ( like an auger), they allow wiring, they are rapidly manufactured (200ml/h) and they are easy to assemble. If the production details are respected and they are properly assembled, there will not be any problem during use ( e.g. the floor creaking).

Prefabricated roof trusses with MiTek connectors are also an optimized and efficient solution for roofs and attics. As opposed to classic carpentry with truss frames where all the processes are carried out on-site by handymen, the prefabricated roof trusses are manufactured more efficiently in the hall: the wood is cut automatically or manually and the MiTek connectors are applied through automatic pressing. The assembly of the roof trusses can be made with or without a crane, depending on the project’s specifications. Roof trusses can also replace the plate over the last level, therefore optimizing certain costs. The prefabrication technology with MiTek connectors is highly versatile and thus, particular surfaces and shapes are achieved much more rapidly and efficiently than in classic carpentry.

When we are talking about prefabrication, an extremely important aspect for a successful project is the correlation between the design and manufacturing, and then the assembly. It is done through specialized design software that optimizes the quantity of wood that is used, also taking into account the transport conditions ( the size of the structural elements) and the assembly conditions. This is why prefabricated constructive solutions should be taken into account starting from the design stage.
Wood vs Brickwork
Compared to the classic brickwork system, a prefabricated wooden structure house is different by the reduced production lead time. From our experience, depending on the equipment level ( shell house, semi-finished or turnkey), a timber frame structure house needs approximately a month to be built and the process is divided into 2 steps: the manufacturing in the hall and the assembly on the site. As a general rule, the production lead time is in inverse ratio with the assembly time. The more polished the house is, delivered from the factory, the less the assembly takes.

In the classic brickwork system, a usual brickwork house has a production lead time of 1-3 months and it can be extended depending on the period of the construction, the availability of the workforce ( which is a current problem), budget planning, and unforeseen expenses that can reach up to 30% of the building’s worth. For a wooden house, the costs are predictable and previously established, with no further surprises. If we refer only to materials, a wooden house is not cheaper than a classic brickwork one, but if we count the longer production lead time and the respective manual labor for brickwork, the costs are the same, in fact, a wooden house becomes cheaper.
Construction works relocate to halls
More than ever, technology allows us to improve each process in the construction of a house and thus we meet the growing demand for houses. More and more European countries are confronted with a crisis in dwellings, and the classic methods for construction are inefficient in solving this problem, not to mention the severe shortage of workforce in this sector. This is why, the future of construction works relocates to halls and more and more companies invest, globally, in prefabrication technologies not only to build simple houses but also apartment buildings or commercial buildings.
Comments